Full Metal Barber - Final
- paulcframe
- May 3, 2018
- 5 min read
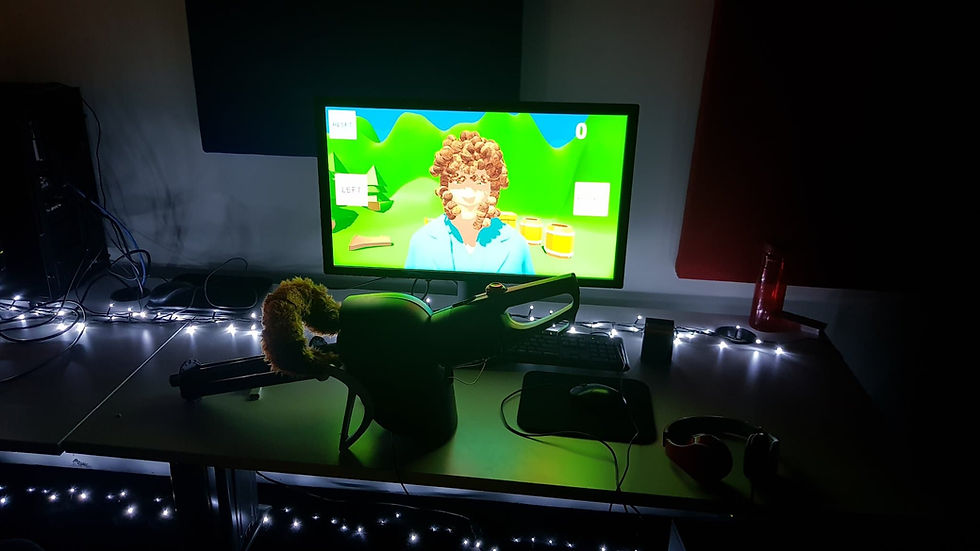
Full Metal Barber has been the first material design project I’ve ever worked on, it has had huge iterations in its design over the weeks the team and I have been working on it. Our initial design was to create a shotgun with a large pair of scissors attached which when you cocked the gun they would open and close. This designed pulley system was overly complicated and a potential hazard to users and people standing by. Since the brief was to create something tailored to showcasing we pivoted into making a mini gun. This brought its own difficulties but was a really fun and engaging project to work on. Our initial concept of the mini gun was to have a huge hulking weapon for people to brandish but for the sole purpose of giving someone a virtual haircut.
Project Management
Although there was no designated project manager for our team “A little off the top” many of the duties fell to me. This was because one team member lived over an hour and a half away and one lived in a one bedroom unit in the city. This left most of the physical side of the guns creation to me as I had the space and tools necessary to get the job done. This certainly was a team effort though, knowing the limitations of every team member gave me the abilities to breakdown the tasks and assign them to not only the person who was best suited to the task but to the team member who was most interested in that side of the project. For example I took on the physical aspect while I assigned one team member to researching, documenting and then wiring the on board Arduino and sensors. As time on the project passed we all found ourselves weaving between the roles and this was a huge benefit to the project as the gun took a huge amount of problem solving to get working at almost every turn it felt like one step forwards two steps back. But while taking on board the limitations of all members and also playing to the strengths of all members we were able to create a fun project both to play and to work on.
Testing Processes – Formulating a testing plan and design changes
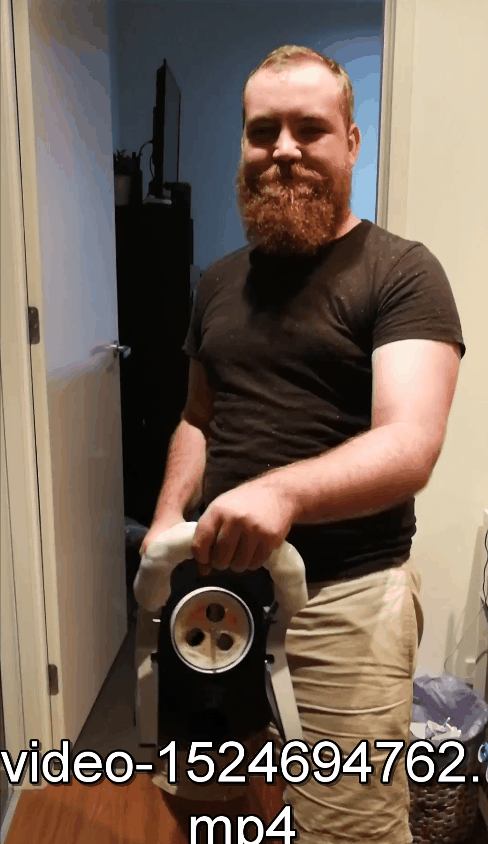
During our planning phase of Full Metal Barber, our decision to find materials at Reverse Garbage made it very difficult to plan out the exact dimensions. This lead our testing plan to be one day a week where we tested the progress of the gun, we used team members and third parties to test the design at each stage and iterated consistently on the design to really focus on making a project that was prime for showcasing. This iteration process really developed my significant skill in fast and reactionary problem solving skills. At every point of the project we were able to roll with the punches and make strong design changes to better the project.
One of our early huge iterations on the project was changing the way we were handling the mouse movement in the game. Originally we were using a Wii mote with a third party program to convert the Wii motion plus accelerometer to mouse position. The more we got this working we found that it was incredibly unreliable. As soon as we found this problem we immediately swapped to using a Arduino Leonardo with the addition of a 5060 gyroscope and accelerometer. Although this still gave us problems it was far more reliable than the Wii mote and was also far easier to mount inside the gun. The other major design change through the project was the integration of spinning barrels by using a drill motor. Unfortunately due to its unreliability we didn’t end up utilising this function for our final showcase at Synergy. The original problem I came across was connecting the spindle of the motor and the PVC base of the barrels. The motor had quite a small spindle and when putting it through with the addition of the torque when turned on the spindle melted the surrounding PVC and lost its traction very quickly. To alleviate this I took the gear set from the original drill and reconnected it to the motor, I then set a bolt in the chuck and threaded it through the PVC tube with a bolt on the other side. This allowed the drill to turn the barrel base; unfortunately this wasn’t the only problem which arose when trying to get the gun to spin. Once I had the gear system working the connection between the motor and the gear system which was just a series of three small plastic clips broke off. This caused the gear attached to the spindle to just spin freely inside the other gears wearing them down. As to not cause any further damage to the gears I needed to find a way to support the gear system and hold it in place. I found a metal piece of fencing support at a local hardware store which had the perfect indentation to support the gears. Unfortunately even with adding a foam support the weight of the barrels still pulled the gears from the spindle. I then had many attempts at hot gluing a bed in which to attach the two and after many failed attempts resorted to using Plastimake and letting it set solid. This was a risky move since there was no going back after that attempt but it was a calculated risk and it paid off. The weight of the barrels even with the gears secure and all internals working perfectly was still just too much for the gun to spin reliably so for our final showcase we decided to not utilise this functionality. Moving forward I would love to get this working more reliably and also look into more use safety by putting a secure shield of laminate to protect the users from the spinning barrels. The final design choice that changed dramatically in the project was the handle. I had originally used the subwoofer which was the housing for the gears and Arduino which had a base attached and by moving this up one set of screws which gave users plenty of room between their hands and the barrel. Unfortunately the weight of the gun snapped this handle after a short while but I was able to use Plastimake to reinforce the handle but the hand feel was horrible. I tried to use a cricket bat grip to give the player a nicer feel to the grip but the handle was far too large and wrapping it around wouldn’t cover enough area. This lead me to using fake fur wrapped around the handle, this felt really good and added to the comical nature of the project and really brought people attention to the game at the Synergy. Full Metal Barber was full of so many constant iterations but our team consistently adapted to the situations and we were able to collaborate together successfully to produce a fun material design project.
תגובות